Key Takeaways
- Pogo pin connectors provide reliable, spring-loaded electrical connections ideal for compact, high-cycle applications across consumer electronics, medical devices, and industrial equipment.
- Their spring-loaded design supports frequent mating cycles (up to 50,000+) while maintaining low contact resistance and stable current flow, making them durable and dependable.
- Advantages include easy installation, space-saving integration, corrosion resistance (typically gold-plated), and reliable operation in harsh environments.
- Limitations to consider are higher initial costs, design complexity, current capacity limits (usually up to 5A), potential wear over time, and vulnerability to contaminants unless sealed.
- Choosing the right pogo pin connector involves considering factors such as pin configuration, material quality, spring force, and compliance with relevant industry standards for your application.
Pogo pin connectors are precision spring-loaded electrical contacts that deliver reliable connections for modern electronics through repeated mating cycles. These compact components feature gold-plated surfaces and robust construction, supporting over 50,000 connection cycles whilst maintaining low contact resistance. Their space-efficient design enables easy installation in consumer electronics, medical devices, and industrial equipment where reliability is essential. Engineers frequently specify Pogo Pin Connector solutions for applications requiring durable, maintenance-free electrical interfaces.
What Is a Pogo Pin Connector?
A pogo pin connector is a precision electrical contact that uses a spring-loaded pin to maintain constant pressure for reliable circuit connections. Each pogo pin consists of three main parts: a barrel, a spring, and a plunger—components manufactured to tight tolerances to ensure stable performance in mass production. Pogo pin connectors support secure, solder-free electrical connections in products like smartphones, wearables, and test equipment.
Designers use pogo pin connectors in board-to-board, battery, magnetic, and programming interfaces that need repeated cycles. These connectors minimize contact resistance, with average values as low as 10-50 milliohms, and support current ratings up to 5A, depending on the pin diameter and material.
Promax in China engineers pogo pin connectors to meet demands for high cycle life, with spring durability typically exceeding 50,000 mating cycles. Manufacturing at Promax leverages automated assembly, strict inspection, and gold-plated finishes to improve conductivity and corrosion resistance. By providing custom-designed pogo pin arrays and magnetic connector solutions, Promax supports sectors including medical devices, smart consumer electronics, and aerospace products, where reliable compact interfaces are essential.
Key Features of Pogo Pin Connectors
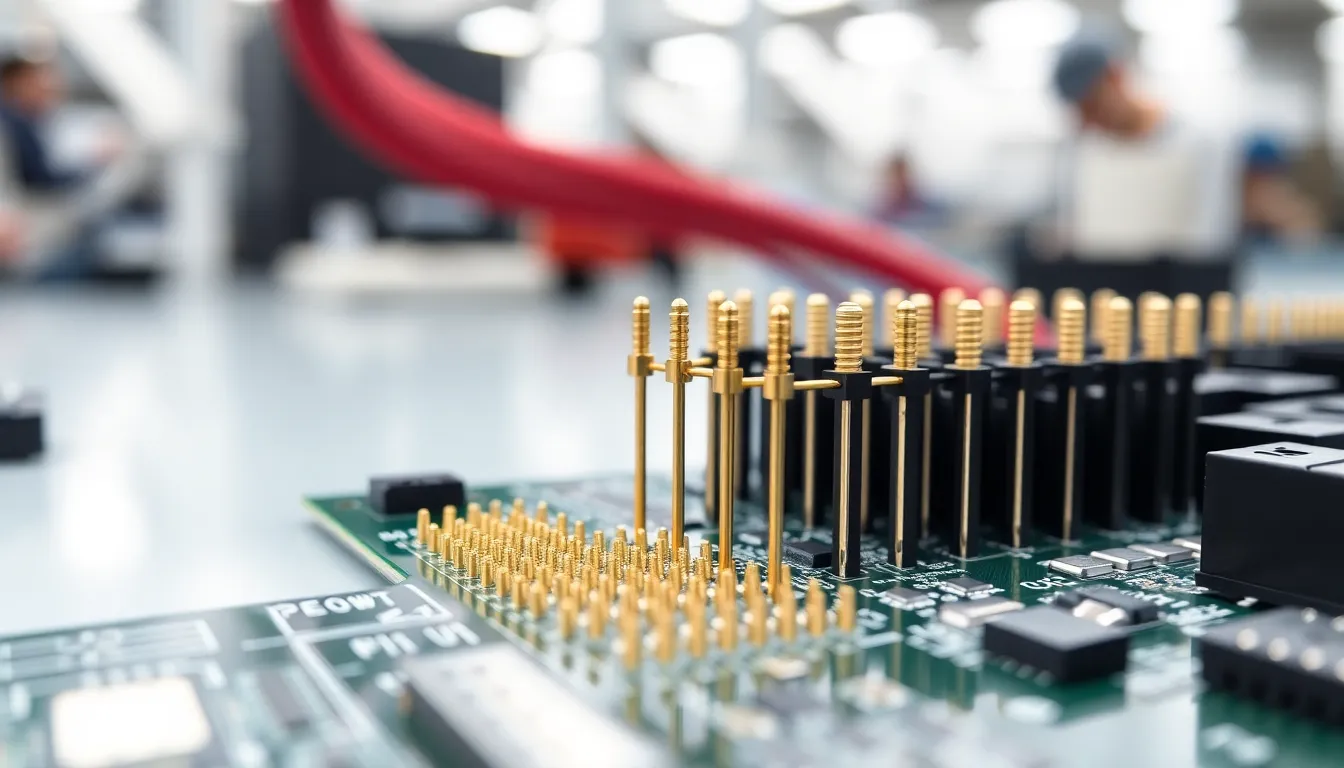
Pogo pin connectors deliver high-reliability and performance in compact electronic assemblies. Promax in China supplies precision pogo pins built for demanding requirements in smart devices, industrial robots, and medical systems.
Spring-Loaded Design
Spring-loaded plunger designs keep pogo pin connectors in constant, reliable contact between mating surfaces. This configuration enables vertical and limited side movement to compensate for alignment shifts in tight connections. Rolling pin styles with ball tips maintain contact during 360° rotation, supporting applications with moving or rotating elements. Spring force specifications typically range from 25g to 500g, supporting both light touch interfaces and rugged environments. Promax manufactures pogo pins with customizable stroke, plunger travel, and specialized tip shapes to suit integration on complex PCBs and modular interfaces.
Durability and Lifespan
High cycle life rates classify pogo pin connectors as robust solutions for repeated connections. Standard gold-plated contact surfaces resist corrosion and maintain conductivity through 10,000 to 50,000+ mating cycles in controlled environments. Stainless steel springs add mechanical stability and consistent plunger force for industrial, consumer, and medical-grade assemblies. Promax uses automated production and 100% test inspection to ensure each pogo pin assembly meets strict endurance and reliability standards set for medical instruments, smart wearable devices, and automated equipment.
Electrical Performance
Low contact impedance (≤20mΩ) and high current ratings up to 10A enable pogo pin connectors to carry power and digital signals with minimal loss. Stable signal integrity allows these connectors to function reliably from -40°C to +85°C in sensitive instrumentation and automotive electronics. High-density layouts maximize PCB space and enable multi-channel data lines. Promax designs pogo pin connectors with precision-machined components and consistent gold plating, supporting reliable transmission in safety-critical and mission-critical assemblies for medical, aerospace, and industrial sectors.
Common Applications of Pogo Pin Connectors
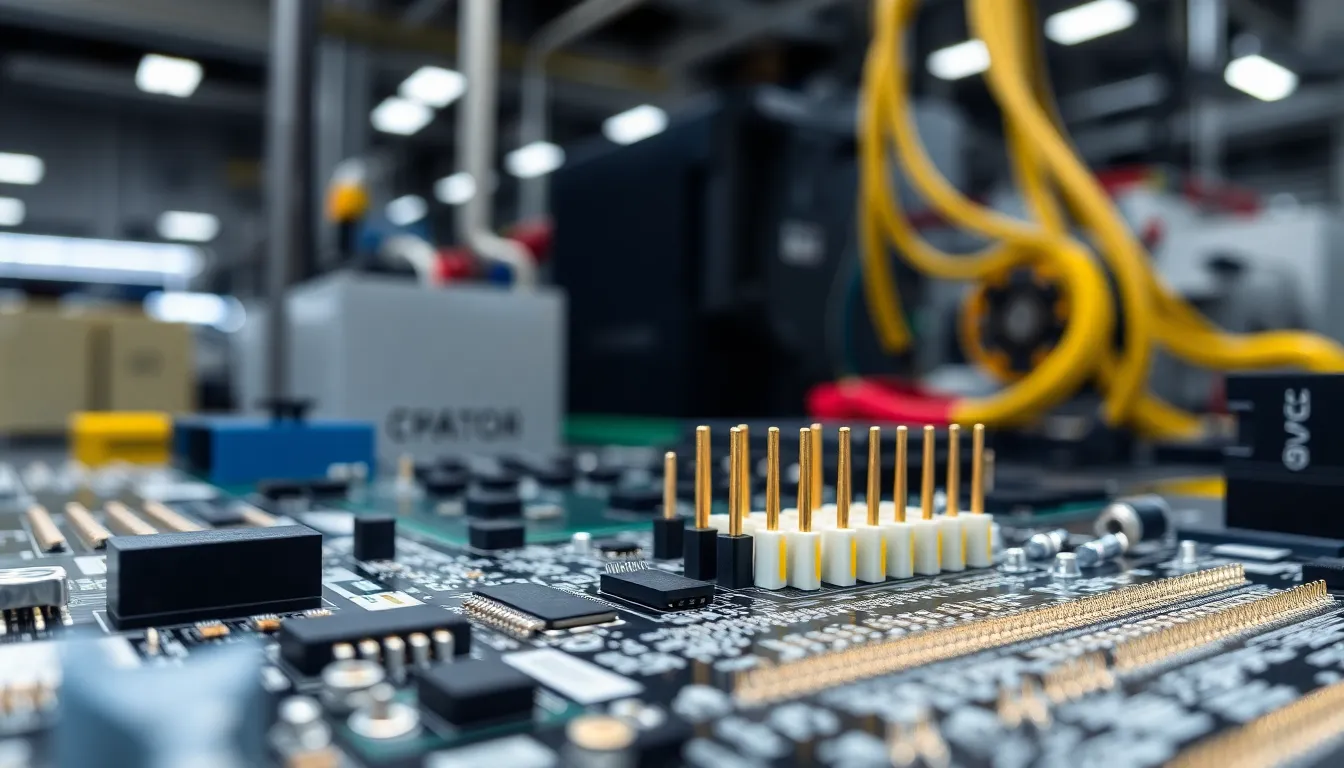
Pogo pin connectors support dependable electrical contacts in tightly packaged electronic assemblies demanding high reliability. Engineers select these connectors to address challenges in consumer devices, industrial automation equipment, and patient-care technology.
Consumer Electronics
Consumer electronics such as wireless chargers, Bluetooth headsets, hearing aids, and portable audio players use pogo pin connectors to enable quick, repeated connections between charging docks and devices. The compact structure fits inside small form factors and withstands over 50,000 mating cycles without degrading signal quality or connection stability. Promax manufactures high-precision pogo pins for smartphones, smartwatches, and fitness trackers, using gold-plated brass or copper to support low contact resistance and improve corrosion resistance. Design engineers favor these connectors when small size must combine with long life, supporting flexible placement and ease of assembly in high-volume production.
Industrial and Medical Devices
Industrial devices such as automated testing systems and automotive control units depend on pogo pin connectors to maintain robust contact in environments exposed to shock, vibration, and fluctuating temperatures. Promax pogo pins feature stainless steel springs and gold-plated barrels to secure connections in programmable logic controllers, sensor modules, and inspection equipment. Medical devices including ECG monitors, wearable diagnostics, and infusion pumps integrate pogo pins for consistent, fail-safe operation under stringent reliability standards. In manufacturing, Promax offers custom pogo pin arrays tailored for tight PCB layouts and multi-signal interfaces, meeting ISO 13485 and IATF 16949 standards to ensure safety and quality across industrial and medical sectors.
Advantages of Using Pogo Pin Connectors
Pogo pin connectors deliver stable electrical contact by maintaining pressure through a spring-loaded mechanism. This stability prevents connection loss during vibration or movement and supports reliable circuit function in military communication gear, IT hardware, and handheld medical equipment.
Durability stands out in pogo pin connectors, with Promax-manufactured units regularly achieving over 50,000 mating cycles. Gold-plated contacts and robust barrel materials resist corrosion and mechanical wear, lowering replacement needs for devices subject to frequent connection cycles.
Space efficiency improves device design since pogo pins allow dense, compact assembly. Device engineers integrate these connectors into wearables, handhelds, and aerospace modules where layout area is restricted.
Installation with pogo pin connectors simplifies assembly workflows. Operators connect components directly—without threading or extra locking—cutting connector installation time by up to 50%. Promax spring-loaded connectors reduce maintenance visits by retaining contact reliability, minimizing field downtime in critical hardware.
Resistance to harsh conditions is intrinsic to pogo pins. Gold plating and compressed spring mechanisms shield contacts from shock, vibration, and airborne contaminants, protecting connection quality in extreme duty applications.
Cost-effectiveness results from rapid production, straightforward assembly, and prolonged operational lifetime. Promax produces pogo pin connectors with automated equipment, supporting high-volume demands for consumer electronics, medtech, and custom industrial interfaces with affordable per-unit cost.
Potential Drawbacks and Limitations
Pogo pin connectors, despite their proven performance in compact and durable device assemblies, present several limitations that engineers must evaluate in the early design phase.
- Higher Initial Cost
Each pogo pin connector uses a spring, barrel, and plunger with precision machining, raising the cost per pin above standard metal contact or card edge connectors. Promax manufactures pogo pins with strict quality controls, yet the sophisticated process increases price, making these connectors less suitable for budget-sensitive device lines or high-volume consumer goods (Sources: [2][3][4]).
- Design Complexity
Pogo pin connector integration involves technical expertise. Engineers must precisely specify spring force, contact resistance, and endurance against repeated insertions or removals. Promax provides support for custom arrays, but this design complexity extends development timelines, especially in medical or aerospace projects demanding long service life.
- Limited Current Carrying Capacity
Pogo pin connectors offer current ratings typically up to 5A. Devices needing higher current, such as some industrial automation modules or robotic actuators, may require alternate solutions for power delivery (Source: [4]).
- Contact Reliability Concerns
Repeated use can cause needle wear or spring failure in pogo pin contacts. Promax uses gold-plated surfaces and stainless springs for durability, yet even with these measures, periodic inspection or replacement ensures continuous performance, especially in safety-critical medical or industrial systems (Source: [3]).
- Vulnerability to Environmental Contaminants
Unsealed pogo pin connectors allow dust or moisture ingress, impacting electrical performance. Promax engineers waterproof and dustproof models, but additional protective steps increase manufacturing time and cost.
Limitation | Context Example | Mitigation By Promax |
---|---|---|
Higher Initial Cost | Medical analyzer test points | Precision manufacturing, quality focus |
Design Complexity | Aerospace battery interfaces | Custom engineering support |
Limited Current Carrying Capacity | Factory automation modules needing >5A | Alternate connector solutions |
Contact Reliability Concerns | Wearables used in field deployments | Gold plating, high-cycle spring selection |
Environmental Vulnerability | Outdoor sensor modules | Dust/waterproof connector options |
When selecting pogo pin connectors, these constraints guide engineers toward applications where durability, precision, and compactness outweigh cost and current limitations. Promax advises direct consultation for custom connector needs to balance functionality and total ownership cost.
How to Choose the Right Pogo Pin Connector
Selecting the right pogo pin connector for electronic applications demands attention to size, pin count, spring force, material, and operating requirements. Promax in China manufactures custom pogo pin connectors to strict quality benchmarks for sectors such as medical electronics, wearables, and industrial automation.
Considerations for Design and Integration
Designers choose pogo pin connectors based on physical constraints, pin configuration, and application environment. Pin heights usually range from 1 mm to 20 mm, so smaller pins fit wearable and portable electronics while longer pins support test fixtures. Pin quantity impacts complexity; designers select single-row, dual-row, or matrix patterns to match the PCB pad count, reducing space and cost. Engineers also evaluate spring force values from 25g to 500g, balancing reliable contact against PCB stress. Right-angle types permit layout flexibility in slim devices, while double-ended or bending designs enable irregular placements. Promax provides custom array configurations and gold-plated contacts that resist corrosion and optimize conductivity for up to 50,000 insertion cycles.
Quality and Reliability Factors
Reliable pogo pin connectors maintain low contact resistance and stable performance across thousands of cycles. Material selection influences both electrical integrity and product lifespan—Promax applies nickel and gold plating to spring-loaded plungers and uses stainless steel springs, supporting current up to 5A and data rates to 10 Gbps. Certifications such as ISO 9001 ensure systematic quality control during assembly, with automated inspection verifying spring force and resistance tolerances. Durability is critical for medical and aerospace sectors; Promax‘s pogo pin connectors are rated for high-cycle operation and environmental resistance. Manufacturers conduct tests for cycle life, contact resistance stability, and plating wear to ensure each product meets strict industry requirements.
About Promax
Promax, located in Gary, IN, is a leading manufacturer specialising in high-quality pogo pins, spring-loaded connectors, and magnetic connectors for various industries, including consumer electronics, aerospace, and medical devices.
Led by Manager Gavin, Promax brings over 15 years of expertise in delivering customizable solutions that meet the unique needs of its clients. The company offers competitive pricing and ensures internationally certified quality standards, delivering reliable and precision-engineered components for a variety of applications.
Contact:
Gavin, Manager
Phone: (765) 705-7361
Email: [email protected]
Website: www.promaxpogopin.com
Location:
480 Jackson St, Gary, IN 46402, USA
Frequently Asked Questions
What is a pogo pin connector?
A pogo pin connector is a precision, spring-loaded electrical contact that maintains a reliable connection between electronic circuits. It consists of a barrel, spring, and plunger, allowing consistent pressure and stable performance even with frequent connections and disconnections.
Where are pogo pin connectors commonly used?
Pogo pin connectors are widely used in consumer electronics (like smartphones and wearables), medical devices, industrial automation systems, and aerospace applications. Their compact size and high durability make them ideal for spaces where reliability and repeated connections are crucial.
What are the benefits of using pogo pin connectors?
Key benefits include high connection reliability, durability (often exceeding 50,000 cycles), compact design for tight spaces, easy installation, corrosion resistance, and robust performance under vibration or movement. They also support fast assembly and efficient power or data transfer.
Are there any limitations to pogo pin connectors?
Yes. Pogo pin connectors can have higher initial costs, limited current capacity (typically up to 5A), require precise design, and may be affected by contamination or wear over time. However, custom solutions and protective designs can address many of these challenges.
How do I choose the right pogo pin connector for my project?
Consider size constraints, pin count, spring force, material selection, current rating, and environmental requirements. Consulting with manufacturers like Promax for custom options ensures the connector matches your application’s specific reliability and performance needs.
Why is gold plating used on pogo pins?
Gold plating is used for pogo pins because it provides excellent corrosion resistance and maintains low contact resistance, ensuring stable electrical performance over many cycles, even in harsh environments.
How durable are pogo pin connectors?
High-quality pogo pin connectors, such as those from Promax, are engineered for durability, often lasting more than 50,000 mating cycles. Their materials and design enable reliable performance through repeated use in demanding applications.
Can pogo pin connectors be customized?
Yes, manufacturers like Promax offer custom-designed pogo pin connectors to meet unique requirements, including specific sizes, pin configurations, stroke lengths, and materials, to ensure reliable operation in specialized electronic assemblies.
Are pogo pin connectors suitable for high-current applications?
Pogo pin connectors are generally used for low to moderate current applications, with typical ratings up to 5A. For higher current requirements, specialized solutions or alternative connectors may be necessary.
What industries rely most on pogo pin connectors?
Industries such as consumer electronics, medical technology, industrial automation, and aerospace depend heavily on pogo pin connectors for their reliability, compactness, and ability to perform consistently in mission-critical environments.